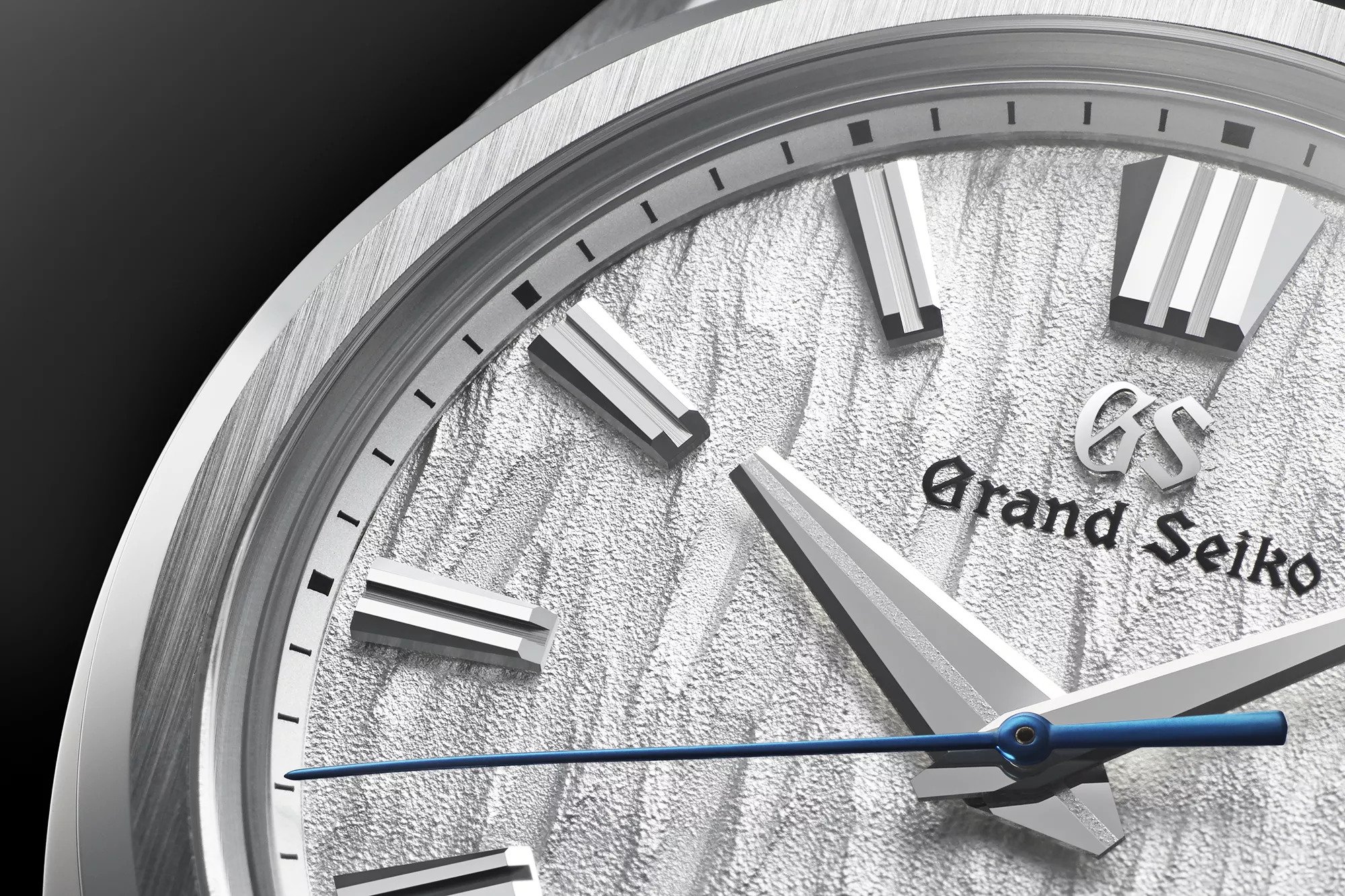
Grand Seiko is often celebrated for its exceptional dial work, which reflects the purest expression of the brand’s distinctly Japanese visual aesthetic. The design of each dial is often based on a unique core theme—regularly pulling from the natural world as a source of inspiration—and it is this theme that informs the selection of colors, textures, patterns, and a number of other details that make Grand Seiko dials so unique.
To make Grand Seiko’s highly detailed dials a reality, skilled craftsmen and women are involved in every aspect of the manufacturing process, from making the metal molds themselves, all the way through to coating, polishing, and final quality inspection.
To get a better sense of just how involved the dial-making process is, today we look behind the curtain at the making of Grand Seiko’s White Birch dial for reference SLGH005.
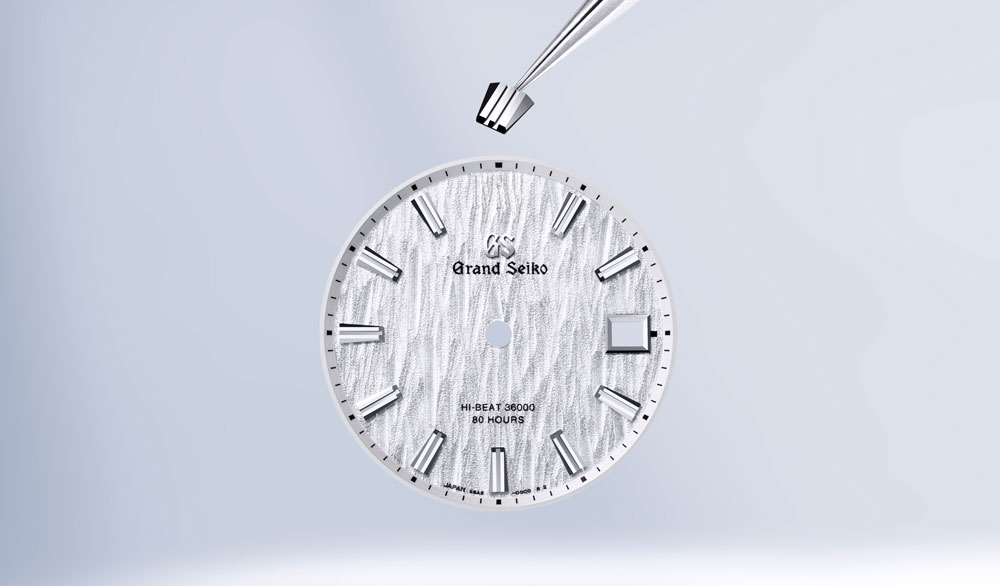
The White Birch dial began as one of several prototypes developed by Grand Seiko’s dial manufacturing team. To execute the notably deep pattern, with its many alternating peaks and valleys, a special mold had to be created—a process that itself required six months of heavy development. Hikaru Matsumoto, a master craftsman who works on the development of Grand Seiko dials, explains the challenge:
“The initial design called for quite deep relief etching, but the available depth that we could obtain was limited by the constraints of the manufacturing process. Having said that, we needed to have the right amount of depth in order to achieve the patterning effect we were looking for. It was a delicate balancing act, and it took us a long time to get it just right.”
With the metal mold settled, work on the dial can begin. Below, we will examine what goes into each step of the dial-making process.
Cutting and Stamping
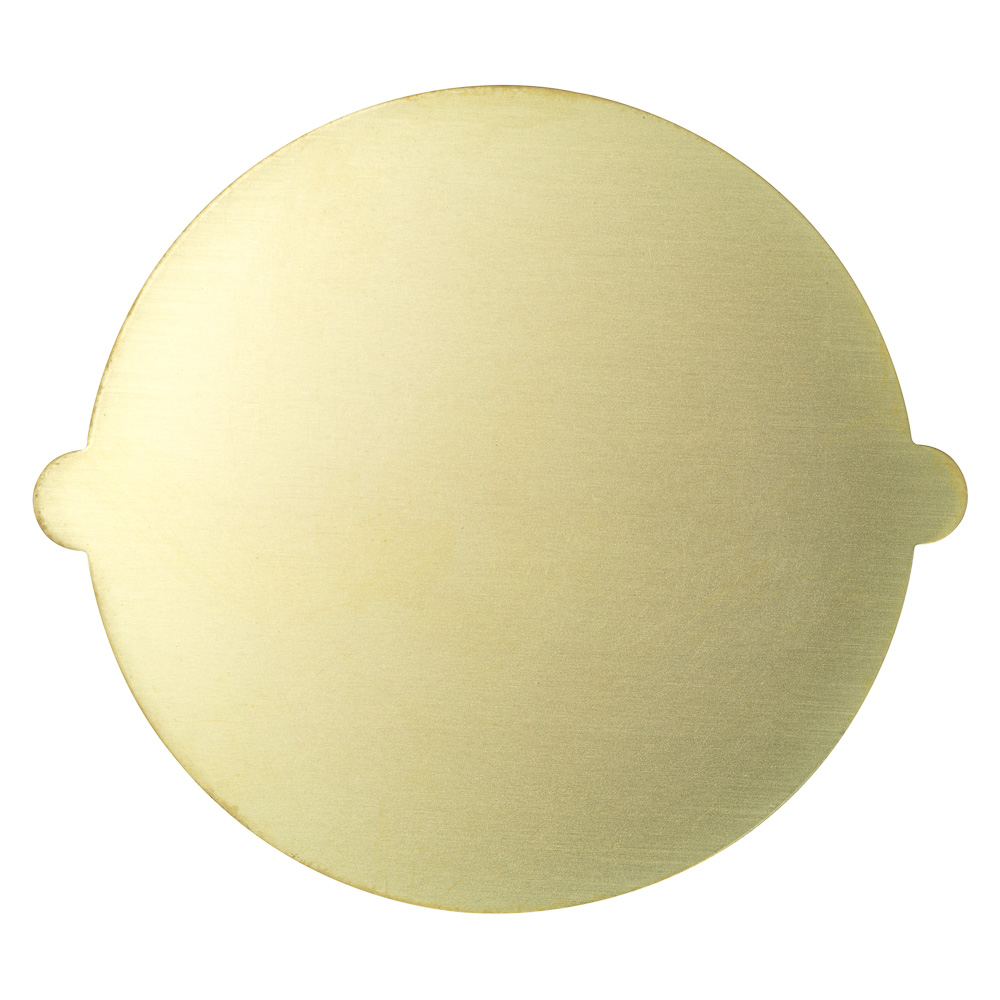
First, the dial base is cut from a piece of brass. Then the dial is pressed with the mold. Normally, a single stamping is sufficient to achieve the desired effect. However, in the case of the White Birch dial, due to the depth of the texture, greater force is necessary to transfer the pattern. This presents a challenge. The required force poses a possible danger to the integrity of the thin dial base (just .5mm), which may crack under heavy pressure. Instead, the pattern is applied via seven low-impact stampings, or press patterning passes to achieve the necessary result.
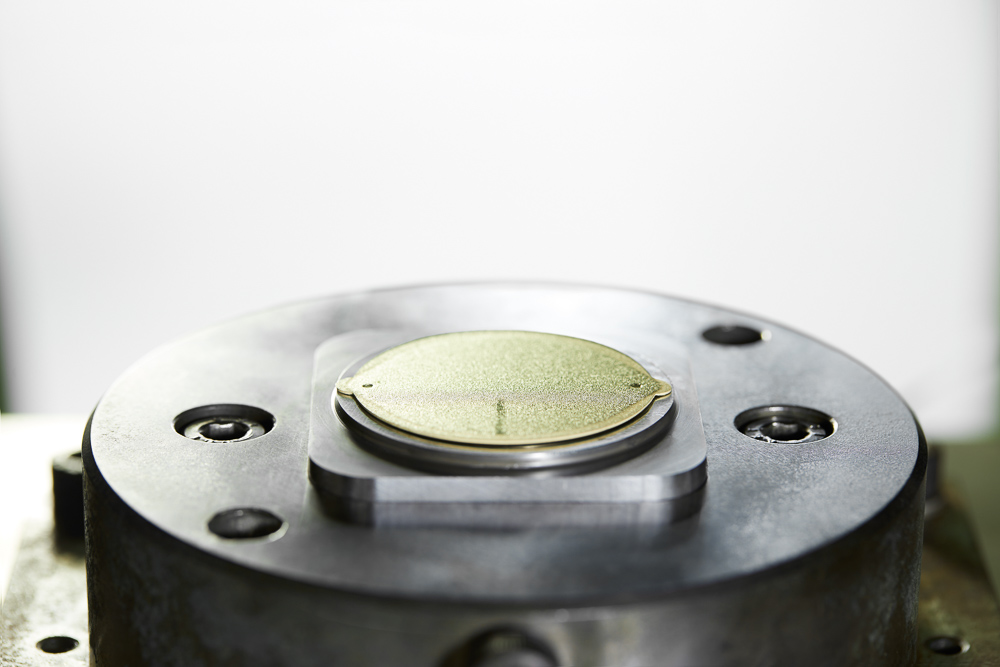
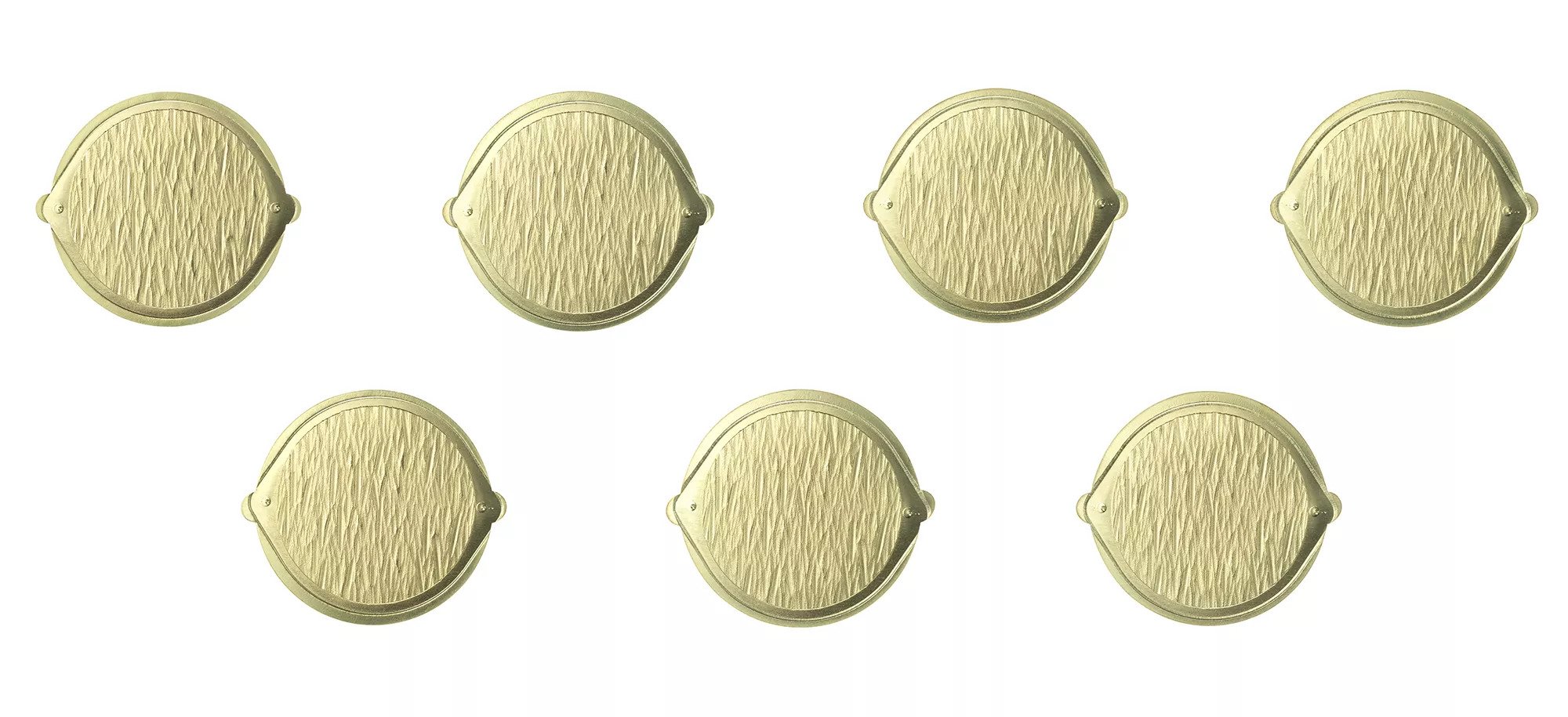
With the transfer of the pattern complete, the base piece is then trimmed down to the size of the dial. Openings for the hands and window are cut, and holes used for mounting the indexes to the dial are punched through. The excess metal around the index holes and date window are shaved off. Finally, the pins that secure the dial in position are attached to the back of the dial.
At this point, each dial goes through a complete quality inspection with a particular focus on curvature and dimensional accuracy. If the dial passes, it is sent to the next phase of its journey—surface finishing.
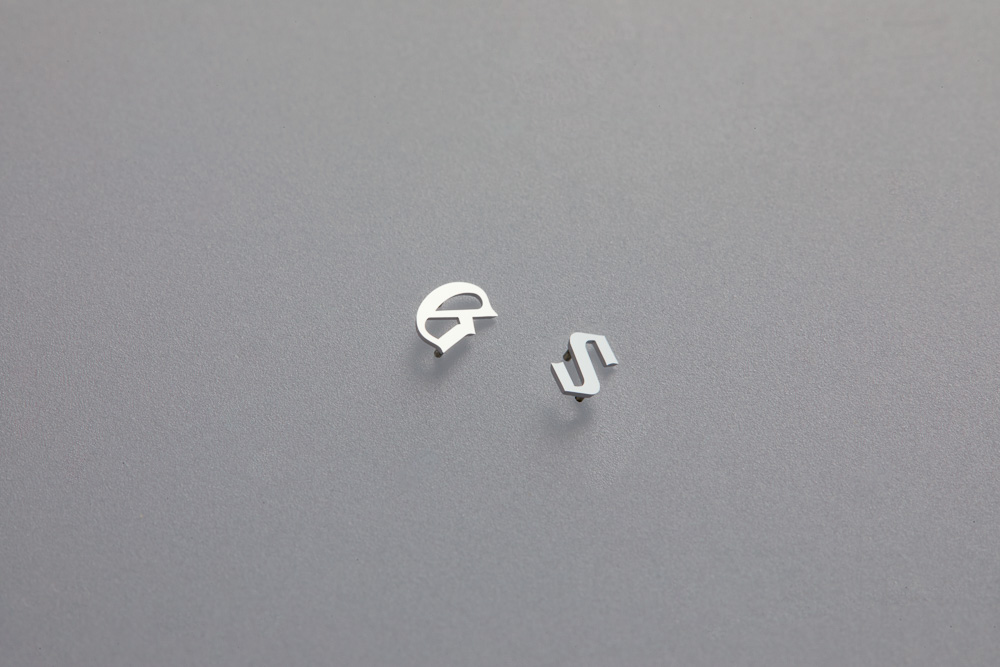
Surface Finishing
Surface finishing is made of four distinct processes: metal brushing, silver plating, undercoating, and wrap coating.
The first step, metal brushing, creates vertical strokes along the dial to add texture. With most dials that feature patterns, the base is usually pre-processed by stripping the top layer prior to this brushing step. With the White Birch dial, however, special consideration was needed to ensure that the stamped pattern wasn’t impacted. Grand Seiko developed a gentler approach to preprocessing to address this issue. Furthermore, the brushing process itself had to be rethought, because it normally requires the use of an abrasive. Grand Seiko developed an approach not needing an abrasive. Additionally, a small brush—about half the size of what is common—is used. Mr. Matsumoto explains the delicate balance of getting this right:
“We have to be careful not to overdo the brushing, as this could make the surface appear too bright. But at the same time, we need a certain level of shine to make the stamped pattern really stand out.”

The dial is then silver plated, and this is followed by a clear undercoat that is added to protect the silver plating and to provide a base for the final wrap coating step. With most Grand Seiko dials, the undercoat is typically the same color as the finished dial, but because the White Birch design calls for silver plating, a clear undercoat is used instead. This step takes special coordination because the silver-plating can impact the appearance of the coating. After undercoating, all dials are inspected closely for blemishes before proceeding to the final process of wrap coating.
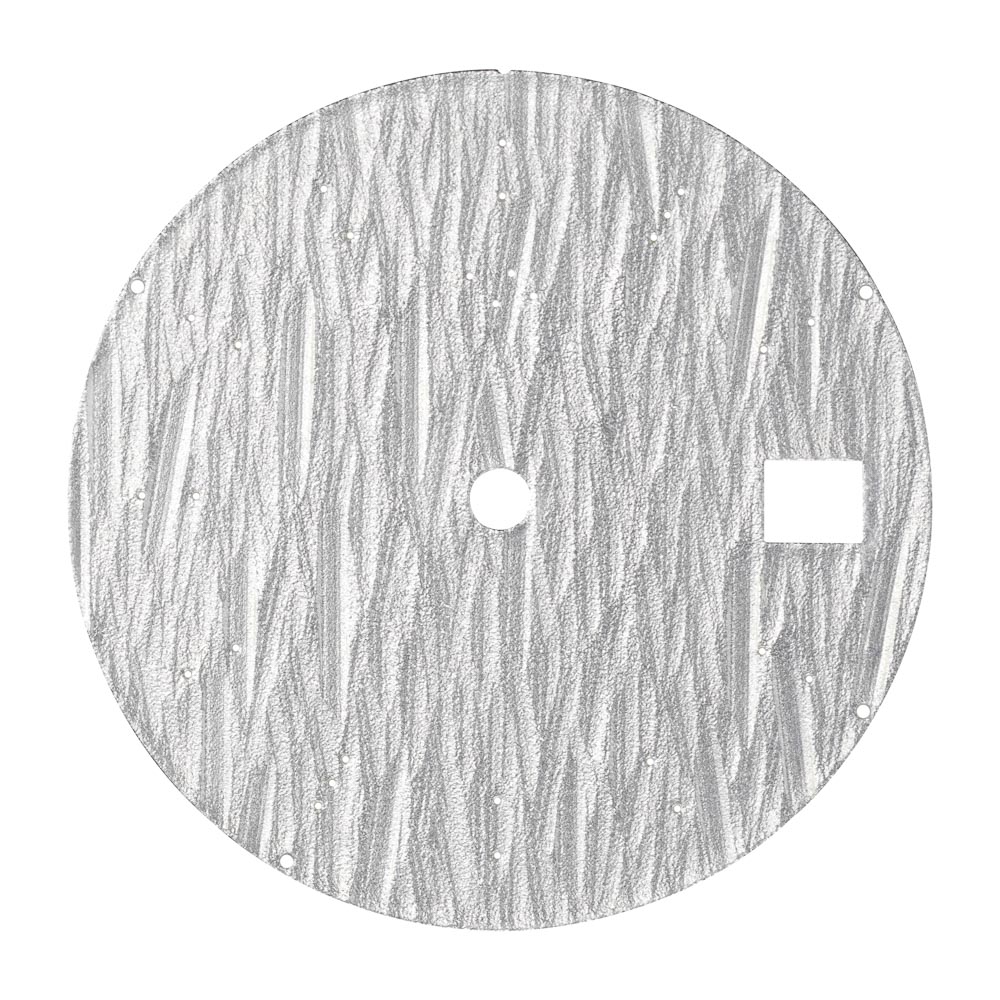
Wrap coating is a highly labor-intensive phase in the process. The first step in wrap coating involves applying a top coat. This is done by adding layers on top of layers of clear coating and allowing each layer to dry before adding more. This is repeated until the stamped pattern is completely covered. Then a preliminary polishing is done to smooth out the thick surface of the top coat. The depth of the pattern requires double the normal quantity of coatings, so a second coating and polishing step is added to the process. Altogether, with the second coating and polishing step, there are about 14 to 15 layers of the coating applied to the dial, which is more than twice the number used on a standard dial.


The finished dial goes through a thorough inspection process, which includes checking and cleaning the previously punched holes. Following this step, details such as the logo, the words “Grand Seiko” and other text are added. The text is applied to the dial multiple times, and it is dried at high temperatures over a long period of time.
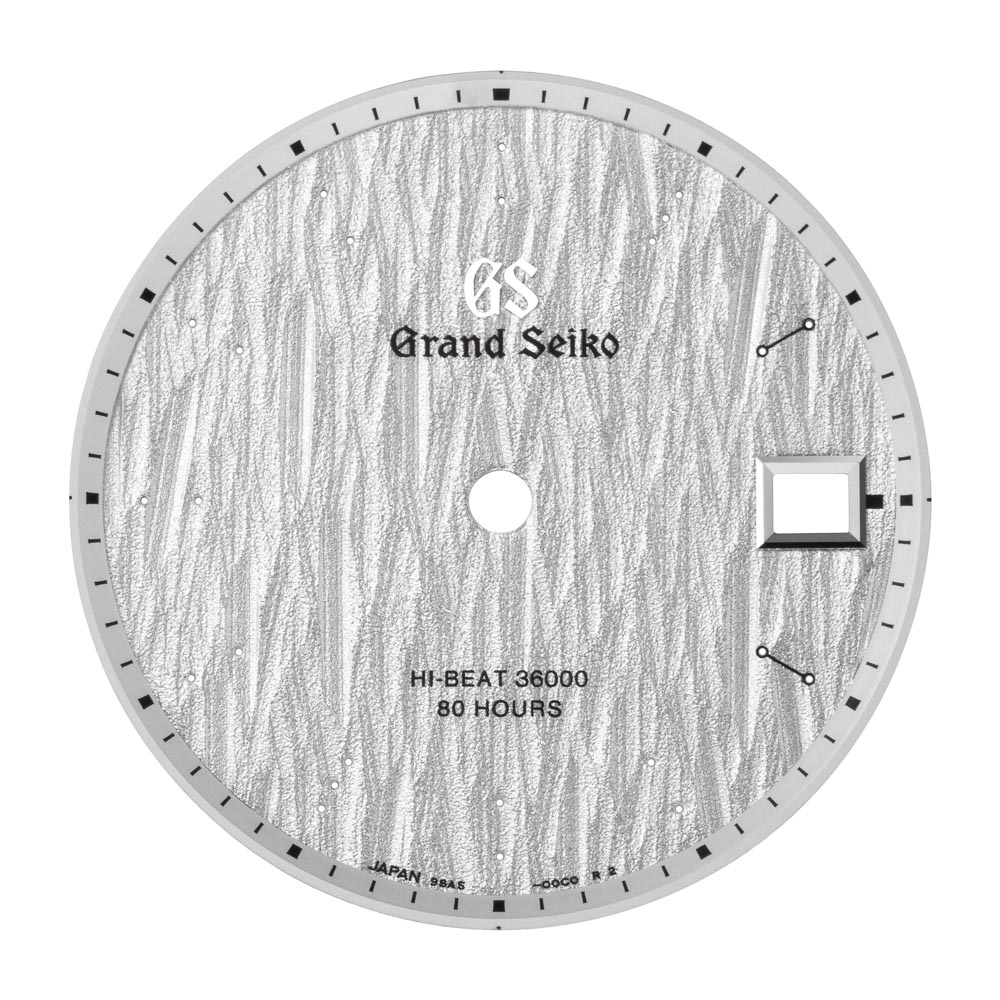
The next step is caulking. This involves the application of the GS logo, the date window frame, and the indexes. Tweezers are used to handle these delicate parts, and they are glued into place. Great dexterity is required here to avoid any potential damage to the dial and its components. This is also when the dial ring is fitted into place and the minute track is printed.

Finally, every dial is meticulously inspected after completion. This involves a finish quality check and a pre-shipment inspection to ensure that nothing but the highest-grade quality leaves the factory. If approved, the dials are complete.